NEWS RELEASE
Editor’s note: Links to video and high-resolution images for download appear at the end of this release.
David Ruth
713-348-6327
david@rice.edu
Mike Williams
713-348-6728
mikewilliams@rice.edu
Student invention gives patients the breath of life
Rice University team’s device automatically squeezes bag valve masks to save lives
HOUSTON – (May 1, 2019) – Natalie Dickman squeezed the bag again and again in an effort to revive a victim of cardiac arrest. After a mere 3 minutes, she could squeeze no more.
“The patient had been down for 30 minutes and there wasn’t much hope, unfortunately,” said the Rice University student, a soon-to-be graduate of the Brown School of Engineering, who was covering a shift with Houston EMS as required by a Rice class in emergency medical techniques. “I was allowed to bag, but they make you switch in EMS settings because they know you won’t be as accurate once you hit that 2-to-3-minute mark. You get really tired.”
She thought about that often over the last year when she and her senior teammates worked at Rice’s Oshman Engineering Design Kitchen (OEDK) to perfect a cost-effective device that automates the compression of manual bag valve masks, which feed fresh air to the lungs of intubated patients.
The senior capstone design team — bioengineering students Dickman, Carolina De Santiago, Karen Vasquez Ruiz and Aravind Sundaramraj, mechanical engineering and computational and applied mathematics student Tim Nonet and mechanical engineering student Madison Nasteff — is known as “Take a Breather.”
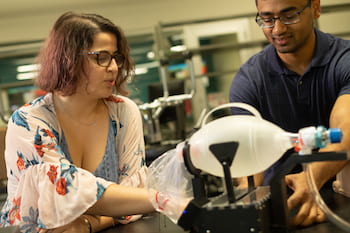
Engineering students Natalie Dickman and Aravind Sundaramraj adjust their automated bag valve mask device at Rice University’s Oshman Engineering Design Kitchen. Photo by Jeff Fitlow
The team has developed a system that compresses the bags for hours, rather than minutes, with settings to feed the right amount of air to adults, children and infants. The device seems simple — a box with paddles that rhythmically squeeze the bulb a programmed amount — but the engineering behind it is not.
The students used a $25, off-the-shelf motor and $5 microcontroller to power and program the rack-and-pinion device made primarily of plastic parts 3D-printed at the OEDK. They hope their use of inexpensive materials and the growing availability of 3D printers will make their machines easy to repair on-site.
They anticipate the device, which cost them $117 in parts to build, will be most useful in low-resource hospitals or during emergencies when there aren’t enough portable ventilators to meet the need.
Dr. Rohith Malya, an assistant professor of emergency medicine at Baylor College of Medicine, brought the problem to the OEDK after witnessing family members at the Kwai River Christian Hospital in Thailand, where he is director of emergency medical services, squeezing intubation bags for hours on end to keep loved ones alive.
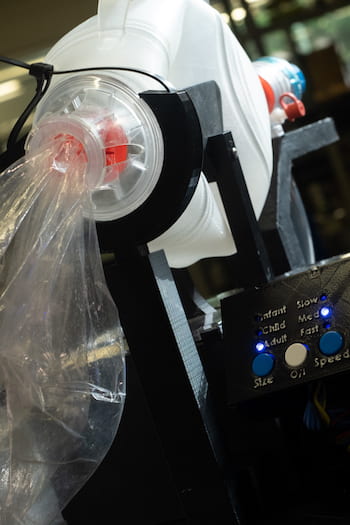
The adjustable bag valve mask device developed by Rice University engineering students has proven able to pump air unassisted for hours on end. Photo by Jeff Fitlow
“There is no reliable ventilation,” said Malya, who spends a month at the hospital every year. “Once we intubate somebody, the family has to bag the patient. But the family will get tired after a day and say, ‘They’re not getting better right now, just pull the tube and see what happens.’ And then the patient dies.”
Malya previously worked with Rice engineering students to develop a syringe regulating pump, and did not hesitate to bring a new idea to the OEDK.
“The bag mask is ubiquitous, like the syringe,” he said. “Nothing has challenged it for 80 years. It’s stood the test of time, it’s reliable and it’s simple. And now we’re adding a modification to the original device so families don’t have to make those decisions.
“This will broaden the access to mechanical ventilation to a tremendous part of the world that doesn’t have typical ventilators,” said Malya, who plans to take the proof-of-concept device to Thailand for field testing next spring.
The device is much smaller than the sophisticated ventilators found in American hospitals and portable versions used in emergency situations. Critically, it has to be able to operate for long stretches. In its most recent test, the team ran the device for more than 11 hours without human intervention.
The students expect another Rice team will build a more robust version next year, and hope it will eventually be manufactured for use in low-resource and emergency settings. They anticipate a better-sealed and filtered box will be more suitable for hot, dusty environments, and said future designs should include more sophisticated controls.
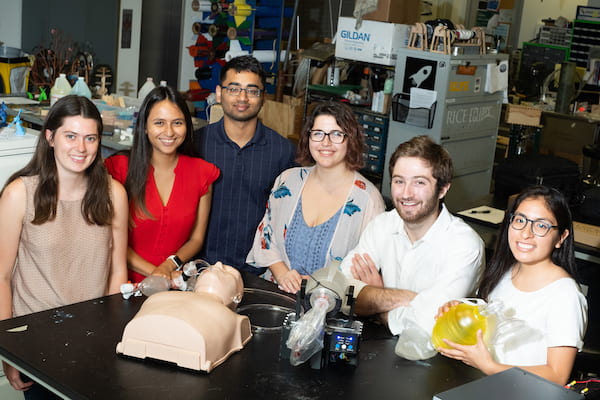
Rice University engineering students developed a bag valve mask compressor to automate the difficult task of feeding fresh air to patients’ lungs, often for hours at a time. From left: Madison Nasteff, Carolina De Santiago, Aravind Sundaramraj, Natalie Dickman, Tim Nonet and Karen Vasquez Ruiz. Photo by Jeff Fitlow
For its efforts this year, the team won two prizes at the school’s annual Engineering Design Showcase, the Willy Revolution Award for Outstanding Innovation and the best interdisciplinary engineering design award. But the real payoff would be seeing the device further developed and deployed around the world.
“If they can get it working fully in that kind of environment, this will be saving lives,” Nasteff said.
-30-
Visit the team’s webpage at http://oedk.rice.edu/Sys/PublicProfile/47585242/1063096.
Follow Rice News and Media Relations via Twitter @RiceUNews.
Video:
Video produced by Brandon Martin/Rice University
Related materials:
George R. Brown School of Engineering: https://engineering.rice.edu
Oshman Engineering Design Kitchen: http://oedk.rice.edu
Images for download:
https://news2.rice.edu/files/2019/04/0506_BREATHE-1-WEB.jpg
Rice University engineering students developed a bag valve mask compressor to automate the difficult task of feeding fresh air to patients’ lungs, often for hours at a time. From left: Madison Nasteff, Carolina De Santiago, Aravind Sundaramraj, Natalie Dickman, Tim Nonet and Karen Vasquez Ruiz. (Credit: Jeff Fitlow/Rice University)
https://news2.rice.edu/files/2019/04/0506_BREATHE-2-WEB-1.jpg
The adjustable bag valve mask device developed by Rice University engineering students has proven able to pump air unassisted for hours on end. (Credit: Jeff Fitlow/Rice University)
https://news2.rice.edu/files/2019/04/0506_BREATHE-3-WEB.jpg
Engineering students Natalie Dickman and Aravind Sundaramraj adjust their automated bag valve mask device at Rice University’s Oshman Engineering Design Kitchen. (Credit: Jeff Fitlow/Rice University)
https://news2.rice.edu/files/2019/04/0506_BREATHE-4-WEB-2.jpg
Rice University engineering student Carolina De Santiago sets up a mannequin to receive air from the automated bag valve mask device she and her teammates designed and built. The team hopes its work will help save lives where and when ventilators are not available. (Credit: Jeff Fitlow/Rice University)
https://news2.rice.edu/files/2019/04/0506_BREATHE-5-WEB-2.jpg
Rice University engineering students Karen Vasquez Ruiz and Tim Nonet adjust the automated bag valve mask device they and their teammates designed as their senior capstone design project. (Credit: Jeff Fitlow/Rice University)
https://news2.rice.edu/files/2019/04/0506_BREATHE-6-WEB-2.jpg
Rice University mechanical engineering student Madison Nasteff adjusts the bag valve mask device designed to automate the process of squeezing the bulb that provides fresh air directly to the lungs of patients. The device could help save people where ventilators are not available. (Credit: Jeff Fitlow/Rice University)
Located on a 300-acre forested campus in Houston, Rice University is consistently ranked among the nation’s top 20 universities by U.S. News & World Report. Rice has highly respected schools of Architecture, Business, Continuing Studies, Engineering, Humanities, Music, Natural Sciences and Social Sciences and is home to the Baker Institute for Public Policy. With 3,962 undergraduates and 3,027 graduate students, Rice’s undergraduate student-to-faculty ratio is just under 6-to-1. Its residential college system builds close-knit communities and lifelong friendships, just one reason why Rice is ranked No. 1 for lots of race/class interaction and No. 2 for quality of life by the Princeton Review. Rice is also rated as a best value among private universities by Kiplinger’s Personal Finance.